Rasterwalze

Die Rasterwalze oder auch Aniloxwalze (engl. anilox roller) dient im Kurzfarbwerk – wie es in der Druckindustrie beispielsweise im Flexodruck, im Offset-Zeitungsdruck oder im wasserlosen Offsetdruck Verwendung findet – der Übertragung der Druckfarbe auf die Druckplattenoberfläche. Sie hat eine zentrale Bedeutung für die konstante und homogene Dosierung der Farbmenge während des Druckvorgangs und gilt daher als Kernelement des Druckfarbwerks.[1][2]
Geschichte und Entwicklung
Anfang des 20. Jahrhunderts bestanden die Farbzufuhrsysteme für den Anilindruck (dem früheren Flexodruck) aus zwei oder mehr Gummiübertragungswalzen, die mit einstellbarem Druck die auf die Druckplatte übertragene Farbmenge dosierten. Das System war nicht sehr präzise und lieferte keine reproduzierbaren Ergebnisse. Bei Tiefdruckverfahren wurden bereits geätzte Kupferwalzen zur definierten Farbabgabe eingesetzt, so dass es naheliegend war, das Prinzip auf den Hochdruck zu übertragen. Problematisch war jedoch die kurze Lebensdauer der Kupferwalzen aufgrund ihrer geringen Härte. 1939 meldete Doug Tuttle, ein Mitarbeiter eines Druckfarbenherstellers, ein US-Patent für eine mechanisch gravierte Stahlwalze zur Farbübertragung an. Da die Handelsnamen für die Anilinfarben der Firma auf das Präfix „-ox“ endeten, nannte er seine Erfindung anilox roller. Die frühen mechanisch gravierten Rasterwalzen hatten quadratische Näpfchen in Form einer umgekehrten Pyramide, die Rasterfeinheit war jedoch durch Werkzeug- und grafische Beschränkungen limitiert.[3]
Die Farbzufuhr erfolgte weiterhin durch Tauchwalzensysteme, die viel Farbe aufnahmen und auf die Rasterwalze übertrugen. Nachteil des Verfahrens war die hohe Tonwertzunahme, die ein dunkleres Bild entstehen ließ. Zur gezielteren Farbdosierung wurden ab den 1960er Jahren Rakelsysteme als Alternative zu den Quetschwalzen eingesetzt. Die zunächst mitläufige Rakel (positiv, < 90°) wurde später durch eine gegenläufige (negativ, > 90°) ersetzt, um eine effizientere Farbübertragung zu gewährleisten.[4] Die Einführung der Rakel bewirkte jedoch einen erhöhten Rasterwalzenverschleiß, die frühen stahlbeschichteten Walzen hielten der Beanspruchung durch die Klingen nicht stand. Zudem boten geätzte Kupferwalzen Raster- und Volumenkombinationen, die mit mechanisch gravierten Walzen nicht möglich waren. So ging man dazu über, die Kupferwalzen mit einer dünnen Chromschicht als Verschleißschutz auszurüsten.[3] Verchromte Rasterwalzen, mit denen Rasterfeinheiten von bis zu 200 Linien pro Zentimeter erzeugt werden konnten, waren viele Jahre lang der Industriestandard im Flexodruck und werden auch heute noch für verschiedene Anwendungen eingesetzt.

Ebenfalls in den 1960er Jahren entwickelte die Harper Corporation eine Rasterwalze mit einer hexagonalen Wabenstruktur, die durch die optimierte Flächennutzung feinere Raster erlaubte. Gleichzeitig trug sie dazu bei, die Schichtdicke der Druckfarbe von damals üblichen 4–7 µm auf 1–3 µm zu reduzieren, wie es bei Tiefdruckverfahren bereits Standard war.[5] Obwohl die Verchromung eine Verbesserung darstellte, war nach wie vor der hohe Verschleiß ein Problem. Die Entwicklung neuer Technologien für das thermische Spritzen führte dazu, dass die Chromwalzen weitgehend durch keramisch beschichtete Walzen mit höherer Oberflächenhärte verdrängt wurden. Die Beschichtung der ersten Keramikwalzen bestand aus einer Aluminiumoxid-Titandioxid-Mischkeramik, in die kein geometrisches Muster eingraviert war. Diese Walzen nutzten die Porosität der Oberfläche, um Farbe aufzunehmen und zu übertragen.[3]
Ende der 1970er Jahre ermöglichten Fortschritte in der Lasergravurtechnologie zusammen mit Walzenschleif- und Poliertechniken die Herstellung lasergravierter Keramikwalzen. Damit konnte die Rasterfeinheit auf über 500 Näpfchen je Zentimeter erhöht werden und es ließen sich neue Kombinationen von Geometrien und Linienrastern realisieren.[3] Ungefähr zur gleichen Zeit wurden Entwicklungen im Bereich der Farbzuführung durch Kammerrakelwerke weiter vorangetrieben. Das geschlossene System ermöglicht die Farbübertragung bei weitaus höheren Druckgeschwindigkeiten, ohne dass sich die Viskosität der Farbe ändert.
Neben Optimierungen der Keramikoberfläche sollte mit der Einführung von Sleeves, einem pneumatisch gespannten Hülsensystem, ein schneller Auftragswechsel ermöglicht werden. Ein Wechsel der Farbbelegung der Druckwerke bringt den Verlust der von der Rasterwalze dosierten Farbvolumina mit sich. Daher war es naheliegend, nicht nur Druckformzylinder, sondern auch Rasterwalzen als einfache Stahlzylinder mit wechselbaren Sleeves auszuführen.[6] Anfang der 1990er Jahre wurden die ersten Maschinen mit Sleeves für Rasterwalzen ausgestattet. Die Sleevetechnologie führte zu einer drastischen Reduzierung der Rüstzeiten und machte den Flexodruck wirtschaftlich wettbewerbsfähiger.[7]
Aufgabe und Funktion

Die Rasterwalze ist das Speichermedium eines Druckfarbwerks, das während des Druckvorgangs konstant eine definierte Farbmenge zur Verfügung stellen soll. Auf der Keramik- oder Chromoberfläche der Walze befinden sich kleine, gleichmäßige Näpfchen (Kalotten), mitunter auch Linien (Haschur) oder wellenförmige Kanäle, die mit verschiedenen Gravurverfahren erzeugt werden. Die nicht vertieften Stellen nennt man „Stege“, die Vertiefungen „Näpfchen“ oder „Zellen“.
Der Farbauftrag erfolgt meist über ein Kammerrakelsystem.[8] Aber auch Tauchwalzensysteme mit zwei oder drei Walzen und Anspülung durch Farbkartuschen sind im Einsatz.[9] Mit Hilfe einer gegenläufigen Rakel werden die Stege von überschüssiger Farbe befreit. Somit verbleibt nur in den Vertiefungen eine definierte Farbmenge. Die Rasterwalze überträgt die Druckfarbe auf die nächste Walze oder, wie im Flexodruck, direkt auf das Klischee, indem sich die Vertiefungen gleichmäßig entleeren. Die Entleerung ist jedoch nie komplett, bei jeder Umdrehung der Walze findet eine Farbdurchspülung innerhalb der Näpfchen statt. Durch die Rotation der Rasterwalze und die damit einhergehende gleichmäßige Farbaufnahme und -abgabe wird das Farbwerk kontinuierlich mit einem definierten und reproduzierbaren Farbvolumen versorgt.
Entscheidende Parameter für die übertragene Farbmenge sind die Geometrie der Näpfchen, insbesondere ihre Öffnung und ihr Volumen, die Materialkomponenten der Rasterwalze selbst sowie die durch das Formgebungsverfahren bestimmte Präzision. Die Auswahl der Rasterwalze sollte je nach Anwendungsgebiet (flexible Verpackung, Wellpappendruck, Etikettendruck usw.) sorgfältig mit dem Lieferanten abgestimmt werden, um sie an Parameter wie Druckfarbe, Beschaffenheit der Druckplatte, Druckträger und Maschinentechnik anzupassen.
Abgrenzung
Manchmal wird fälschlicherweise der Druckformzylinder im industriellen Tiefdruck als „Rasterwalze“ bezeichnet. Das ist historisch bedingt: Am Ausgangspunkt für ein rotativ arbeitendes Hochdruckverfahren standen einfach gestrahlte oder aufgeraute Walzenoberflächen. Die Farbübertragung war jedoch nicht ausreichend homogen und unkontrollierbar. Darum wurden die Erfahrungen aus dem Tiefdruck genutzt, der im industriellen Bereich mit näpfchengravierten Chromwalzen arbeitet. Daher sind die ursprüngliche Walzenart, das Gravurverfahren und vor allem das Prinzip der rotativen kontinuierlichen Näpfchen-Entleerung ähnlich. Im Tiefdruck ergibt aber die Rasterung auf dem Druckformzylinder das Druckbild. Die Rasterwalze hat – im Gegensatz zum Tiefdruck-Druckformzylinder – nicht die Aufgabe, ein Druckbild direkt auf den Bedruckstoff zu übertragen.
Rasterwalzenarten
Der Grundkörper einer Rasterwalze besteht aus Stahl, Aluminium oder faserverstärktem Kunststoff. Nach Art der Walzenoberfläche werden zwei Walzen unterschieden, die Chromrasterwalze und die Keramikrasterwalze. Letztere werden in der Regel beim Druck mit niedrigviskosen Farben im Flexodruckverfahren eingesetzt, dagegen finden sich Chromrasterwalzen vorwiegend in Beschichtungswerken, da sich durch die geringere Anzahl von Näpfchen ein höheres Schöpfvolumen erzielen lässt.[10]
Chromrasterwalzen
Die ursprüngliche Bauart der Rasterwalze war die Chromrasterwalze. Der Walzenrohling besteht aus Stahl oder Edelstahl, auf den eine Kupferschicht galvanisiert wird. Nach der Gravur wird, ebenfalls galvanisch, ein Schutzverchromung zur Erhöhung der Verschleißfestigkeit aufgebracht. Der Name Chromrasterwalze bezieht sich auf die äußerste Schutzschicht.
Chromrasterwalzen haben sich jahrzehntelang in Druckwerken mit 3-Walzensystem im Quetschdruck bewährt. Bei Druckwerken mit Rakel ist dagegen der Verschleiß recht hoch und die Lebenszeit dadurch kurz. Rasterweiten bis zu 200 Linien pro Zentimeter (L/cm) sind möglich. Die Gravur ist ein wichtiger Faktor für dosierte und übertragene Volumen und sollte daher präzise erfolgen. Die Näpfchen auf der Chromrasterwalze werden mechanisch durch Prägewalzen, elektromechanisches Schlagen mit einem Diamanten, durch Ätzen oder – wie bei Keramikrasterwalzen auch – mittels Lasergravur erzeugt (vgl. Gravurverfahren). Während die Chromrasterwalze ein hohes Volumen der Näpfchen realisiert und als sehr beständig in Bezug auf die Farbübertragungseigenschaften gilt, hat sie eine deutlich geringere Lebensdauer als die Keramikwalze.
Keramikrasterwalzen
1979 waren die ersten lasergravierten Keramikrasterwalzen verfügbar,[11] die eine höhere Oberflächenhärte und damit eine längere Funktionsdauer als die Chromwalzen boten.
Der Walzenrohling besteht meist aus Stahl[2] oder in Leichtbauweise zur Verringerung der Massenträgheit aus Aluminium oder kohlenstofffaserverstärktem Kunststoff. Die Keramik auf Basis von Chrom(III)-oxid (Cr2O3) wird mittels Plasmabeschichtung auf die Oberfläche aufgebracht. Die hohe Partikelgeschwindigkeit macht eine Haftschicht zwischen Grundkörper und Chromoxid-Keramik überflüssig. Einige Hersteller verwenden bei hohen Anforderungen an die Langlebigkeit und Temperaturbeständigkeit eine Nickel-Chrom-Trägerschicht. Nach der Beschichtung erfolgt eine Feinbearbeitung durch Schleifen oder Läppen, anschließend wird mittels Lasergravur das gewünschte Raster eingraviert. Je nach Anforderungen werden dafür verschiedene Lasertechnologien eingesetzt (vgl. Abschnitt Lasergravur). Abschließend werden die Walzen nochmals feingeschliffen, um Schlackespitzen zu entfernen und die Stege zu glätten (Finishing).[12] Da auch die Oberflächenenergie der Keramik die Farbübertragung beeinflusst, wenden einige Hersteller weitere Verfahren zur Oberflächenveredelung an.[13][14]
Keramikrasterwalzen sind hochverschleißfest und werden überall da eingesetzt, wo eine exakte Farbübertragung über einen langen Zeitraum gefordert ist.[15] Mit ihnen können Rasterweiten bis zu 600 Linien/cm erzielt werden. Nachteil ist der höhere Preis gegenüber der Chromwalze.
Gravurspezifikationen

Die wesentlichen Größen zur Beschreibung des Leistungsvermögens von Rasterwalzen sind:
- Lineatur [L/cm] oder Rasterweite [µm]
- Tiefe [μm] und Flankenwinkel [°]
- Gravurwinkel [°]
- Steg/Napf-Verhältnis [1:x]
- Volumen [cm³/m²] oder [µm]
Alternativ können andere Größen, die sich aus den genannten ergeben, wie die Stegbreite oder das Tiefe/Öffnungsverhältnis der Näpfchen zur Charakterisierung herangezogen werden. Daneben gibt es weitere Parameter wie die Form der Näpfchen und das Verhältnis zur Feinheit des Klischees, die die Übertragung des Druckmediums und damit die Qualität des Druckbildes beeinflussen.
Lineatur – Rasterweite
Das auftragbare Farbvolumen wird neben der Form und Tiefe wesentlich durch die Anzahl der Näpfchen bestimmt. Diese werden auf einer definierten Bezugsstrecke in Winkellage gezählt, so dass die Lineatur in Linien pro Zentimeter (Linien/cm) oder, im angloamerikanischen Maßsystem, in Linien pro Zoll (L/in) angegeben wird. Die Rasterweite gibt Auskunft über den Abstand der Vertiefungen zueinander und wird in Mikrometern angegeben. Mit beiden Angaben ist auch die Breite der Näpfchen und die der Stege festgelegt.
Übliche Rasterfeinheiten von Chromrasterwalzen liegen bei maximal 200 L/cm, sie erzielen höhere Volumina als Keramikrasterwalzen. Rasterfeinheiten von Keramikrasterwalzen liegen bei 500 bis 600 L/cm. Die Entwicklung tendiert zu höheren Rasterfeinheiten, jedoch haben sie in der praktischen Anwendung bisher keinen Nutzen.
Gravurtiefe und Flankenwinkel
Die Gravurtiefe bestimmt bei festgelegter Lineatur das mögliche Napfvolumen, sie wird in Mikrometer gemessen. Eine tiefe Gravur bedeutet nicht notwendigerweise ein hohes Volumen, durch eine andere Form und Größe der Näpfchen kann sie das gleiche theoretische Volumen aufweisen wie eine flache Gravur.
Der Flankenwinkel, angegeben in Grad, ist der Winkel zwischen den Schenkeln der pyramidenförmigen Näpfchen. Je flacher die Gravur, desto größer ist der Flankenwinkel. Ein steiler Flankenwinkel ergibt eine bessere Entleerung und kann daher ein höheres Volumen bieten. Durch Variation des Flankenwinkels bei gleicher Rasterweite und Gravurtiefe wird gezielt auf das Volumen Einfluss genommen.[16]
Gravurwinkel

Der Gravurwinkel beschreibt die Winkellage relativ zur Walzenachse und wird ebenfalls in Grad angegeben. Weil sich nur viereckige oder sechseckige Geometrien geschlossen auf einer Zylinderoberfläche unterbringen lassen, betragen die üblichen Gravurwinkel 90° bzw. 45° bei quadratischen Zellen und 30° bzw. 60° bei hexagonalen Zellen (vgl. Abbildung).
Bei Rakelbetrieb haben Winkellagen von 45° und 60° einen deutlichen Vorteil, weil sie mit der Spitze zu Walzenachse stehen. Die Rakel ist kontinuierlich abgestützt und die Spitzenlage ermöglicht ein sanftes Befüllen und Entleeren der Näpfchen während der Rotation. Die hohe Packungsdichte bei der 60°-Winkellage sorgt für einen homogeneren Farbauftrag und findet daher am häufigsten Anwendung. Bei Übertragung von Lacken, Leim und Klebstoffen wird dagegen eher die 45°-Winkellage eingesetzt, weil sich damit ein höheres Übertragungsvolumen erzielen lässt.
Für einige Anwendungen sind auch 70°- oder 75°-Winkellagen beliebt geworden, die sich durch gestreckte Näpfchen mit längeren Stegen senkrecht zur Walzenachse ergeben. Da eine solche Struktur weniger Stege beinhaltet, lassen sich damit höhere Farbvolumina übertragen. Sie eignet sich daher besonders für Linien und Vollflächen in der Wellpappenindustrie.[17] Den vergleichsweise flachen, bootsförmigen Näpfchen wird zudem ein optimiertes Entleerungsverhalten, eine bessere Laufleistung bei höheren Geschwindigkeiten und eine effizientere Reinigung zugesprochen.[18]
Steg/Napf-Verhältnis
Die Stege bieten die nötige Rakelauflage beim Abstreichen der Farbe, ihre Breite und Form haben somit einen entscheidenden Einfluss auf die Farbübertragung und das Rakelverhalten. Wichtig für die Dichtheit zwischen Rakel und Stegen und einen geringen Messerverschleiß ist das Finishing zur Glättung der Oberfläche. Es wird empfohlen, dass mindestens 70 % der Stegfläche Kontakt zum Rakelmesser haben und die Zellwände im Kontaktbereich eine Dicke von mindestens 3 µm aufweisen.[12] Um die Farbverteilung auf der Walze zu vergleichmäßigen und den Druckaufbau während des Rakelns zu verringern, können die Stege zwecks Austausch zwischen den einzelnen Zellen durchbrochen sein (communicating cells).
Die Öffnung der Näpfchen stellt die Kontaktfläche der Druckfarbe zum Klischee dar. Je größer deren Durchmesser ist, desto homogener kann das Klischee eingefärbt werden. Stegbreite und Öffnungsweite stehen im Steg/Napf-Verhältnis zueinander. Eine Gravur mit 200 L/cm hat eine Zellbreite von 50 µm. Betragen sowohl Stegbreite als auch Öffnungsbreite 25 µm, ist das Verhältnis 1:1. Da für die Einfärbung nicht der Steg verantwortlich ist, muss die Farbe aus der 25 µm breiten Öffnung über eine nicht eingefärbte Stegbreite von 25 µm auf dem Klischee verteilt werden. Das Druckbild ist folglich umso poröser, je größer die Stegbreite im Verhältnis zur Öffnungsbreite ist; optimal für eine ruhige Einfärbung ist ein minimales Steg/Napf-Verhältnis.
Im angelsächsischen Sprachraum wird häufig das Verhältnis von Tiefe zu Öffnung der Näpfchen zur Charakterisierung herangezogen. Dieses lässt sich aus Lineatur, Steg/Napf-Verhältnis und Gravurtiefe ermitteln.
Volumen

Das Volumen einer Rasterwalze bezieht sich auf das Raumvolumen der Zellen unterhalb der Stegauflage. Am geläufigsten ist die Angabe in Kubikzentimetern pro Quadratmeter (cm³/m², entspricht μm), im amerikanischen Standard billion cubic microns per square inch (BCM/in²; 1 BCM/in² = 1,55 cm³/m²). Alternativ kann das spezifische Volumen in g/m² oder ml/m² angegeben werden.
Die Näpfchen auf der Walzenoberfläche bestimmen durch ihre Geometrie und Verteilung das Schöpfvolumen. Sie kontrollieren die Menge des Druckmediums, das durch die Walze aufgenommen, zum Klischee weitertransportiert und wieder auf die Oberfläche abgeben werden kann. Trägt die Rasterwalze mehr Näpfchen, ergibt sich bei konstanter Stegbreite ein höherer Steganteil und damit ein geringeres Schöpfvolumen. Die Volumenangabe ist dennoch eine theoretische Größe und nicht identisch mit der tatsächlich übertragenen Farbmenge. Unterschiedliche Zellformen können bei gleicher Rasterweite und identischem Volumen variierende Entleerungen bewirken. Zusätzlich haben Faktoren wie rheologische Eigenschaften der Farbe, Oberflächenspannung, Druckbeistellung, Geschwindigkeit, Bedruckstoff etc. einen Einfluss auf das wirksame Volumen der Rasterwalze.
Näpfchenform
Die verschiedenen Gravurverfahren bei Chrom- und Keramikrasterwalzen bedingen Formen mit unterschiedlichen Eigenschaften in Bezug auf das Volumen und Entleerungsverhalten. Die (elektro-)mechanisch gravierten Näpfchen einer Chromrasterwalze haben meist die Form von Spitz- oder Stumpfpyramiden. Während die Spitzpyramide zu mangelhafter Entleerung und zu einer höheren Verschmutzung neigt, führt die Stumpfpyramide zu verbesserten Resultaten. Mit steiler Flanke und breitem Boden weist sie die beste Entleerung auf und erzielt das höchste Volumen.
Bie den lasergravierten Näpfchen auf Keramikwalzen wird zwischen Kugelkalotte, Spitzkalotte (ähnlich einem Kegel mit gerundeter Spitze) und U-Shape unterschieden. Die schlechteste Entleerung hat die Spitzkalotte, sie neigt zudem am ehesten zur Verschmutzung. Die Kugelkalotte zeigt ein besseres Entleerungsverhalten, bietet aber ein geringeres Volumen. Eine optimale Entleerung bei gleichzeitig hohem Volumen wird durch die U-Form erzielt.
Verhältnis zur Rasterweite des Klischees
Der kleinste Rasterpunkt des Klischees sollte immer größer sein als das Rasternäpfchen auf der Walze, so dass auch das kleinste Element einen stützenden Steg bei Überrollung der Rasterwalze vorfindet. Ansonsten taucht der Rasterpunkt in das Näpfchen ein, nimmt zu viel Farbe auf und führt durch Überfärbung zu einem unsauberen Druckbild oder zu unerwünschten Effekten, z. B. dem Moiré-Effekt. Während früher die Rasterweite der Rasterwalzen nur zwei- bis dreimal feiner war als die des Klischees und damit unzulängliche Einfärbungen feinster druckender Elemente hingenommen wurden, setzte man später die Größe eines Näpfchens mit einem Steg maximal gleich der Größe des kleinsten zu druckenden Elementes.[19] Daraus ergibt sich, dass die Lineatur der Rasterwalze um den Faktor 5 bis 6,5 höher sein muss als die des Klischees. Beispielsweise sollte bei einer Lineatur des Klischees von 48 L/cm die Walze eine Lineatur von mindestens 240 L/cm aufweisen. Auch die Winkellage der Gravur im Verhältnis zu der des Klischees ist zu beachten; ein ungünstiges Verhältnis kann ebenfalls Ursache für eine Moiré-Bildung sein.
Gravurverfahren
Elektronisch-/mechanische Gravur
Mit konventionellen Gravurmethoden werden ausschließlich Chromwalzen bearbeitet:
- Molettieren: Mit einem Rändelwerkzeug, der Molette, auf deren Oberfläche die Gravur als Matrize vorgefertigt ist, wird sie in die Kupferschicht oder direkt in den Stahl eingeprägt. Danach erfolgt die Schutzverchromung.
- Elektronisch geschlagene Gravur: Mit einem elektronisch gesteuerten Diamantstichel in der gewünschten Pyramidenform werden gezielt Näpfchen eingeschlagen. Gravurtiefe und Steg/Napf-Verhältnis können gezielt beeinflusst werden. Der Diamant ermöglicht durch seine hohe Härte, steile Flankenwinkel zu erzeugen.
Mechanisch gravierte Walzen sind auch heute noch in Gebrauch, werden aber hauptsächlich für die Beschichtung verwendet; mit sehr groben Walzen werden Leim und Stärke aufgetragen.[20] Ihr Nachteil ist, dass sie trotz der Verchromung mit der Zeit verschleißen. Da sich bei mechanisch erzeugten Näpfchen aufgrund ihrer breiten Öffnung der größte Teil des Volumens im oberen Teil befindet, verlieren sie deutlich an Volumen, wenn sich die Tiefe nur um wenige Mikrometer reduziert, was zu einer spürbaren Abnahme der Druckdichte führt. Mechanisch gravierte Rasterwalzen sind bezüglich der Rasterfeinheit auf rund 200 L/cm beschränkt, da es physikalische Grenzen dafür gibt, wie klein sich ein Rändelwerkzeug fertigen lässt.[21]
Lasergravur
Keramikwalzen sind im Vergleich zu Chromwalzen deutlich härter und spröder und können daher nur schwer mechanisch graviert werden. Sie werden mittels Lasergravur mit CO2-Lasern, YAG-Lasern und seit den frühen 2000er Jahren auch mit Faserlasern bearbeitet. Auch Chromwalzen werden inzwischen oftmals lasergraviert, da sich das Verfahren flexibel zur Erzeugung unterschiedlicher Oberflächenstrukturen einsetzen lässt. Die kontaktlose Lasergravur ermöglicht eine gezielte Gestaltung der Näpfchengeometrie und der Schöpfvolumina. Da sich das theoretische Übertragungsvolumen in gewissen Grenzen unabhängig von der Rasterfeinheit einstellen lässt, kann das Farbabgabe- und -aufnahmeverhalten der Zellen anforderungsspezifisch optimiert werden.
Zunächst wurden CO2-Laser zum Gravieren verwendet. Der Laserstrahl lässt die Keramikschicht schmelzen und teilweise verdampfen. Dabei wird ein Kraterrand erzeugt, der bei Wiederholen des Vorganges anwächst, so dass ein Steg entsteht. Beim Erkalten des Materials bildet sich eine einige Mikrometer dicke, dichte und sehr harte Keramikschicht (Recast). Diese erhöht einerseits die Verschleißfestigkeit der Walze[22] und senkt durch die Bildung einer geschlossenen Oberfläche die Verschmutzungsneigung. Andererseits resultieren aus dem Umschmelzen der Keramik relativ breite Stege und Unebenheiten auf der Oberfläche, die die Druckqualität mindern und den Rakelklingenverschleiß erhöhen. Die „Punktgröße“, auf die der Strahl des CO2-Lasers fokussiert werden kann, ist durch seine feste Wellenlänge von 10,6 µm nach unten begrenzt, die maximal erzielbaren Rasterfeinheiten liegen bei rund 400 L/cm.[21]
Für anspruchsvolle Druckaufträge mit bestimmten Hintergrundfarben und Volltonflächen, die eine feine Gravur mit höherer Farbdichte erfordern, wird ein „Multi-Hit“-Verfahren eingesetzt. Anders als bei der Single-Hit-Technologie, bei die Näpfchen jeweils „in einem Schuss“ gebrannt werden, wird beim Multi-Hit-Verfahren jede Zelle durch mehrere Laserpulse erzeugt und so ein höheres Volumen erzielt. Zugleich werden dadurch die Näpfchenwände sauberer, schärfer und gleichmäßiger als bei Standardgravuren.[17] Aus physikalischen Gründen ist die Gravurtiefe jedoch begrenzt, da sonst unter anderem keine Farbspaltung mehr stattfindet.
Um feinere Gravuren für kontrollierte Farbaufträge zu erzeugen, werden seit Ende der 1990er Jahre YAG-Laser eingesetzt, die Rasterfeinheiten bis zu 600 L/cm ermöglichen. Infolge der höheren Energiedichte erfolgt die Gravur dabei überwiegend durch direktes Verdampfen des Materials. Das Ergebnis ist eine wesentlich konsistentere und gleichmäßigere Gravur mit klaren Konturen und ohne nennenswerte Rückstände (Recast) sowie die Erzeugung einer kapillaren Oberfläche. Durch die verbesserte Kopplung ist es außerdem möglich, tiefer zu gravieren und so ein größeres Näpfchenvolumen zu erzielen.[21] Wegen der stark konischen Form der Näpfchen mit einem großen Tiefe/Öffnungsverhältnis geht das jedoch zulasten des Farbabgabeverhaltens.[3] Entsprechend neigen YAG-lasergravierte Rasterwalzen auch zu einer schnellen Verschmutzung und sind schwer zu reinigen. Ein weiterer Nachteil der YAG-Technologie ist der schnelle Verschleiß der Walzen, der umso höher ist, je feiner die Stege sind.
Seit 2002 werden auch Faserlaser verwendet, die durch ihre hohe Intensität im Fokus besonders feine Strukturen erzeugen können. Die Laserstrahlen weisen ein schmalbandiges Spektrum auf, haben eine hohe Strahlqualität und ermöglichen daher höchste Rasterfeinheiten von über 750 L/cm. Die Näpfchen sind weniger konisch und an der Unterseite stärker abgerundet, was eine bessere Farbabgabe bewirkt und höhere Volumina bei gleicher Rasterweite erlaubt.[3] Faserlaser erzeugen im Vergleich zu YAG-Lasern sehr gleichmäßige Strukturen sowie glatte Napfwände und Stege mit geringem Verschleiß. Zudem können moderne Faserlaser 50.000 bis 60.000 Näpfchen pro Sekunde gravieren, während die Gravurgeschwindigkeiten von CO2-Lasern mit 10.000–15.000 Näpfchen/Sekunde wesentlich niedriger sind.[20] Weitere Vorteile des Faserlasers sind ein geringer Energieaufwand, eine kompakte Bauweise und ein hoher Wirkungsgrad. Nachteil ist der vierfach höhere Preis im Vergleich zum CO2-Laser und die Einschränkung, nicht alle Materialien abtragen zu können.[23]
Weitere Verfahren
Neben den genannten existieren weitere Verfahren zur Oberflächenstrukturierung, die vorwiegend im Tiefdruck verwendet werden und bei Rasterwalzen eher selten sind:
- Ätzen der Kupferoberfläche nach Maskenauftrag
- Helio-Klischographie: Der Helio-Klischograph arbeitet ebenfalls mit einem Diamantstichel, der jedoch eine Schwingbewegung vollzieht. Die Näpfchen werden mittels eines elektromagnetischen Gravursystems aus der Oberfläche herausgeschnitten.[24]
- Allgemeines Aufrauen der Walzenoberfläche durch Sandstrahlen
Einsatzgebiete
Rasterwalzen sind in verschiedenen Druck- und Beschichtungsverfahren ein wichtiges Element zur Übertragung von Flüssigkeiten, wie Farbe, Lack, Leim oder Klebstoff. Abhängig vom verwendeten Übertragungsmedium und dem gewünschten Druckprodukt ist das entsprechende Druckverfahren auszuwählen. An die jeweils eingesetzten Rasterwalzen werden dabei verschiedene Anforderungen gestellt.
Flexodruck
Lineatur Rasterwalze [L/cm] | Zellvolumen [cm³/m²] | Übertragene Farbmenge (trocken) [g/m²] | Motiv |
---|---|---|---|
500 | 2,9 | 0,3 | High-Quality-Raster |
400 | 5,0 | 0,5 | Raster |
300 | 7,5 | 0,7 | Rasterflächen |
220 | 9,0 | 0,9 | Rasterflächen und Weiß |
140 | 12,0 | 1,2 | Weiß |
Tiefdruck | 1,2 |
Im hochqualitativen Flexodruck beim Bedrucken von Kunststofffolien, Papier, Karton, Geschenk- und Tissuepapier dient die Rasterwalze als Übertragungselement für niedrigviskose Farben wie Lösemittel-, Wasser- und UV-Farben. Bedingt durch das direkte Hochdruckverfahren existiert nur ein Zwischenschritt bei der Farbübertragung: Die Rasterwalze überträgt die Druckfarbe auf das Klischee (die Druckplatte), das dann direkt auf den Bedruckstoff druckt. Daher sind die Anforderungen an die Rasterwalze in Bezug auf Genauigkeit und Reproduzierbarkeit der Farbabgabe sehr hoch.
Das Farbvolumen der Rasterwalze muss auf das jeweilige Druckmotiv abgestimmt werden (vgl. Tabelle). Die für die Farbgebung erforderliche Gesamtmenge der Farbe wird durch Auswechseln gegen eine anders strukturierte Rasterwalze mit dem jeweils gewünschten Volumen angepasst. „Eine für alle Produktionsprozesse und Bedruckstoffe gleich gut geeignete Rasterwalze gibt es nicht.“[8]
Im Flexodruck werden in der Regel Rasterwalzen mit Lineaturen von 120 bis 600 L/cm eingesetzt. In vielen Fällen wird eine hexagonale Zellform im 60°-Winkel bevorzugt.[2]
Rollenoffset-Zeitungsdruck
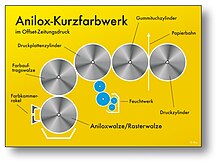
Im Offsetdruckbereich werden für den Zeitungsdruck, der geringere Anforderungen an die Einfärbequalität stellt, teilweise Anilox-Kurzfarbwerke eingesetzt. Diese haben im Vergleich zu konventionellen Offset-Farbwerken weniger Walzen, da niedrigerviskose (dünnflüssigere) Farben eingesetzt werden, die eine zügige Übertragung erfordern. Eines der wichtigsten Qualitätskriterien für die Rasterwalze ist hier eine lange Lebensdauer. Sie muss eine konstante Farbabgabe über mehrere hundert Millionen Zylinderumdrehungen gewährleisten, da sie – im Unterschied zum Flexodruck – fester Bestandteil des Farbwerks ist. Sie ist dem speziellen Maschinentyp genau angepasst und dosiert immer die gleiche Farbmenge. Viele Druckmaschinenhersteller stellen ihre Rasterwalzen selbst her. Meist werden lasergravierte Keramikwalzen mit Näpfchen- oder Haschurstruktur verwendet, wobei in die Haschurtiefen oftmals zusätzlich kleine, flache Näpfchen eingraviert werden. Die genaue Beschaffenheit ist oft Firmengeheimnis oder wurde patentiert.
Da Keramikwalzen durch ihre hydrophile und poröse Oberfläche eine Anlagerung von Farbe und den Transport zurück in den Farbkasten begünstigen, sind Chromwalzen für den Offsetdruck prinzipiell besser geeignet. Dennoch kommen wegen der längeren Lebensdauer vorwiegend Keramikrasterwalzen zum Einsatz.[25] Die Rasterweite solcher Rasterwalzen liegt bei etwa 60 L/cm.
Wasserloser Offsetdruck
Im wasserlosen Offsetdruck wird die Farbabgabe der Rasterwalze und damit die Schichtdicke im Druckprodukt über eine exakte Temperaturführung reguliert. Daher muss die Rasterwalze temperiert werden: Je wärmer deren Oberfläche ist, desto höher ist die Farbschichtdicke. Geringe Wandschichtdicken und hohe Wasserdurchflüsse gewährleisten eine effiziente Wärmeabfuhr. Es werden lasergravierte Keramikwalzen mit sehr dünnen Keramikschichten (maximal 0,1 mm) und darunterliegenden Kunststoffsegmenten verwendet. Die genaue Beschaffenheit wird selten in vollem Umfang veröffentlicht; das gilt insbesondere für die Temperaturregelung der Rasterwalze. Beim wasserlosen Offsetdruck wird wegen der höheren Viskosität der Druckfarben eine niedrigere Rasterfeinheit (ca. 40 L/cm) verwendet.
Beschichtung und Veredelung
In Beschichtungswerken im Tiefdruck kommt die Rasterwalze bei der Übertragung verschiedener Grundierungen, Beschichtungen und Klebstoffe zum Einsatz. Die physikalischen Eigenschaften der Beschichtung bestimmen, wie das Material mit dem gravierten Zylinder in Kontakt gebracht wird. Da die Beschichtungsmedien eine vergleichsweise hohe Viskosität aufweisen, eignen sich Chromwalzen am ehesten, da sie ein höheres Volumen bieten können und die glatte Oberfläche die Abgabe des Mediums begünstigt. Wegen ihrer längeren Lebensdauer werden – wie auch im Rollenoffset-Zeitungsdruck – dennoch häufig Quetschwalzen mit Keramikoberfläche genutzt.
Lackierwerke werden zur Veredelung von Druckprodukten verwendet und sind immer mit einem Trocknersystem verbunden. Gerade im Bogenoffsetdruck ist die Veredelung mit Lacken oder mit Metallicfarben in der Inline-Weiterverarbeitung – das Lackierwerk liegt innerhalb der Druckmaschine im Anschluss an den eigentlichen Druckprozess – sehr verbreitet.[26] Der Lack wird entweder über ein Tauschwalzen- oder über ein Kammerrakellackwerk dosiert, die zentrale Konstruktion ist in ihrer Funktionsweise einem Flexodruckwerk sehr ähnlich. Die aufgetragene Lackmenge hängt vom Schöpfvolumen und dem Entleerungsverhalten der Rasterwalze ab. Um die Dosierung zu ändern, ist gegebenenfalls ein Wechsel der Rasterwalze nötig. Zwei bis drei Rasterwalzen mit unterschiedlichen Schöpfvolumina im Austausch reichen üblicherweise aus.[26] Bei Tauchwalzensystemen kann die übertragene Lackmenge in gewissen Grenzen über den einstellbaren Walzenspalt (zwischen Tauch- und Rasterwalze) oder über eine geschwindigkeitskompensierte Tauchwalzensteuerung reguliert werden; die Dosierung sehr geringer Lackmengen ist allerdings nicht möglich. Außerdem neigt das offene System eher zum Schäumen und Spritzen.[27]
In Lackierwerken sind Keramikrasterwalzen mit einer hexagonalen Gravur im 60°-Winkel standard. Die offene Linienstruktur des Gravurtyps Haschur bietet demgegenüber den Vorteil, dass durch die umlaufenden Rillen (meist im 45°-Winkel) weniger Stege das Übertragungsverhalten beeinflussen. Damit besteht ein höheres Lackangebot an der Oberfläche, was eine geringere Gravurtiefe zulässt. Eine zusätzliche, flachere Gegengravur im 70°-Winkel ermöglicht eine gleichmäßigere Lackverteilung.[28] Rasterwalzen in Lackierwerken verwenden Rasterfeinheiten von 10 L/cm bis 180 L/cm.
Für Metallicfarben, Duftlacke oder Matteffekte werden grobe Pigmente, teils Plättchen oder Kapseln verwendet, die sich in ihrer Größe und Form stark voneinander unterscheiden. Das sollte bei der Rasterwalzenauswahl bedacht werden, weil das zu übertragende Pigmentkorn immer kleiner sein muss als die Näpfchenöffnung.[28] Ansonsten schwimmen zu große Pigmentkörner oder -agglomerate oben auf der Gravur und zermahlen (d. h. sie werden nicht einwandfrei übertragen oder sogar zerstört) oder sie setzen sich in den Näpfchen fest und verkleben dort, wodurch sich das Schöpfvolumen verringert.
Reinigung
Unabhängig von der Qualität der Druckfarbe oder der Leistungsfähigkeit der Rasterwalze werden die Näpfchen beim Druckvorgang nie vollständig entleert. Beim Flexodruck werden lediglich 40 % des Mediums auf die jeweiligen Substrate übertragen, bis zu 60 % verbleiben in den Näpfchen, wovon ein gewisser Teil dort antrocknet.[29] Solche Reste und Schmutzpartikel, z. B. durch Abnutzung von Rakelmessern, verhindern die definierte Übertragung des Druckmediums und wirken sich negativ auf die Druckqualität aus. Verunreinigungen lagern sich bevorzugt am Boden der Näpfchen und am Stegrand ab. Dies beeinflusst das Entleerungsverhalten und hat eine Verbreiterung der Stege zur Folge, was auch als Verschleiß verkannt werden kann.
Üblicherweise werden die Walzen unmittelbar nach jedem Druckgang gereinigt. Auch sonst sind die tägliche Reinigung sowie eine regelmäßige zusätzliche Tiefenreinigung für eine möglichst lange Nutzungsdauer unumgänglich. Insbesondere der Trend zu schnell trocknenden Druckfarben verschiebt die Reinigungszyklen zu kürzeren Intervallen.[29]
Die üblichen Arten der Reinigung umfassen chemische, mechanisch-abrasive und physikalische Methoden. Das Reinigungsverfahren ist an den Grad der Verschmutzung und die Art der verwendeten Walze, insbesondere Material und Lineatur, anzupassen. Die Reinigungsdauer hängt vom Druckmedium und dessen Zustand, dem Reinigungsmedium, der Temperatur und, bei der mechanischen Reinigung, der Friktion ab. Weitere Faktoren bei der Wahl des Reinigungsverfahrens sind die Kosten von Geräten und/oder Verbrauchsmaterialien, Umweltschutzbestimmungen sowie die Möglichkeiten zur Durchführung des Reinigungsprozesses innerhalb sowie außerhalb der Druckmaschine.[29]
Chemische Reinigung
Bei der chemischen Reinigung kommen Waschlösungen zum Einsatz, mit deren Hilfe Ablagerungen gelöst und anschließend unter Hochdruck mit Wasser entfernt werden. In einer geschlossenen Anlage wird die langsam rotierende Walzenoberfläche mit einer temperierten Chemikalie benetzt, die nach Einwirkung entfernt und gefiltert wird. Anschließend werden die gelösten Schmutzpartikel und Rückstände der Reinigungsflüssigkeit mittels einer Sprüvorrichtung mit Wasser entfernt und abtransportiert. Dabei sind die vorgegebenen Temperaturen und Durchlaufzeiten für die jeweiligen Waschlösungen korrekt einzuhalten.
Dieses Verfahren findet Anwendung bei starken Verschmutzungen und Walzen mit hohen Lineaturen (400 L/cm und mehr). Art und Konzentration des Reinigungsmittels müssen auf das jeweilige Walzenmaterial abgestimmt werden, wobei der pH-Wert eine entscheidende Rolle spielt. Insbesondere Aluminium und Stahl können durch den Einsatz ungeeigneter Reinigungsmittel geschädigt werden; auch Chromoberflächen werden durch einige Laugen und starke Säuren angegriffen. Keramikwalzen sind in der Regel auch gegenüber hochaggressiven Reinigungsmedien beständig.
Mechanische Reinigung
Bei der chemischen Reinigung können Bürstensysteme den Waschprozess unterstützen, sie kommen vor allem bei der manuellen Säuberung zum Einsatz. Der Ablösevorgang und der Abtransport von Verschmutzungen wird dabei durch Friktion beschleunigt. Für keramische Walzen wird rostfreier Stahl als Borstenmaterial verwendet, für chrombeschichtete Walzen Messing.
Für Rasterwalzen mit niedriger Lineatur eignen sich mechanisch-abrasive Verfahren, bei denen die Walzen mittels Druckluft mit Trockeneis, Natriumhydrogencarbonat oder Kunststoffgranulat gestrahlt werden. Beim Einsatz ist darauf zu achten, den Aufstrahldruck und die Partikelgröße des Strahlmittels auf die Näpfchen-Spezifikation abzustimmen, um eine Schädigung der Näpfchenwände und Ablagerungen des Reinigungsmediums in den Näpfchen zu verhindern. Zudem müssen die Walzen nach der Behandlung gut abgespült werden. Das Aufstrahlen von Reinigungsmedien gehört zu den effektivsten Reinigungsverfahren und bietet außerdem die Möglichkeit, Walzen innerhalb wie außerhalb der Druckmaschinen zu reinigen. Wird auf die Demontage der Walzen verzichtet, besteht allerdings die Gefahr der Verschmutzung der Druckmaschine, da sich die Mittel über den eigentlichen Reinigungsort hinaus verbreiten.[29]
Physikalische Reinigung
Ultraschallreinigung
Bei der Ultraschallreinigung rotiert die Walze in einer Reinigungslösung und die über den Ultraschall eingebrachte Energie führt zur Bildung mikroskopisch kleiner Dampfblasen, die beim Aufprall auf die Walzenoberfläche durch den äußeren Druck implodieren (Kavitation). Dabei entstehen Druckwellen mit hohen Druckspitzen, die eingetrocknete Reste von Druckfarben und Beschichtungsmedien „absprengen“. Die Ultraschallbehandlung ist eine relativ kostengünstige Option zur Reinigung von Rasterwalzen, kann jedoch bei unsachgemäßer Anwendung zur Beschädigung der Näpfchen innerhalb kürzester Zeit führen.[29]
Laserreinigung
Das Prinzip der Laserreinigung beruht darauf, dass ein kurz fokussierter Laserpuls mit hoher Intensität auf die Walzenoberfläche trifft und die Schmutzschicht infolge der Energieabsorption verdampft. Schmutzpartikel und Reste des Druckmediums werden mithilfe einer Absaugvorrichtung entfernt. Durch Variation der Pulsfrequenz lässt sich die Laserleistung auf das Walzenmaterial abstimmen und der Wärmeeintrag regulieren, um eine thermische Überbeanspruchung der Walze zu vermeiden. Scanbreite sowie Vorschub- und Umdrehungsgeschwindigkeit sind weitere Parameter, die den Energieeintrag und damit die Abtragsleistung bestimmen.[30]
Das Verfahren zeigt gute Reinigungsergebnisse bei schwierig zu reinigenden Substanzen wie Wasserfarben und 2K-Farben sowie bei hohen Lineaturen, bei denen andere Reinigungsverfahren an ihre Grenzen stoßen. Allerdings erfordert die richtige Einstellung des Lasers auf Rasterwalzen mit unterschiedlichen Rasterweiten und die zu entfernenden Substanzen relativ viel Zeit, Erfahrung und Know-how. Die Laserreinigung kommt ohne Chemikalien aus, erfordert keine Nachreinigung und ist für die Inlinereinigung geeignet (z. B. bei schwer zugänglichen Rasterwalzen im Wellpappendirektdruck).[30] Den hohen Investitionskosten stehen vergleichsweise geringe Betriebskosten gegenüber, da nur elektrische Energie und keinerlei Verbrauchsmaterialien wie Reinigungsmedien oder Druckluft benötigt werden.[29]
Qualitätskontrolle
Altersbedingt und nutzerbedingt ergeben sich durch Verschleiß und Verschmutzung Veränderungen an der Form der Näpfchen und auch der Steganteil nimmt zu. Eine fortan schlechtere Entleerung der Farbe führt zu einer mäßigen Einfärbung mit geringerem Volumen. Dazu sollte mit geeigneten Messgeräten Parameter wie Schöpfvolumen, Rasterzahl, Steganteil, Näpfchentiefe, Stegbreite/-öffnung und Steg-/Öffnungs-Verhältnis kontrolliert werden. Besonders wichtig in diesem Zusammenhang sind das Schöpfvolumen und der Steganteil. Durch die Dominanz der Keramikrasterwalze auf dem Markt, haben sich hierfür die Messgeräte etabliert. Einzusetzende Geräte heißen:
- Konfokalmikroskop (Angaben über Näpfchentopologie sowie ein optisches Bild mit der Struktur mit unendlicher Tiefenschärfe)
- Interferometer (Angaben über Näpfchentopologie, WYKO)
- Optische Walzenmikroskope
- Pipettierverfahren (Armi, Urmi 1, Volugraph, Ravol-Tester)
- Fluorescence (Urmi 2)
- Laser Scanning Microscope (Lasertec, Leica)
- Kapazitive Messung (Microspace)
- Capatch (Steinhardt)
- Abtastnadel, Volumenformel mit Mikroskop
Interferometrische Messung
Die Bilderfassung erfolgt mit einem Weisslichtinterferometer, welches Bilddaten auswertet und in 3D-Darstellung Angaben zum Volumen und der Tiefe erzeugt. Ähnliche Geräte heißen konfokale Mikroskope, optische Mikroskope und Interferometer.
Konfokalmikroskop
Es handelt sich hierbei um ein 3-dimensionales Höhenmodell, das die Oberfläche der Rasterwalze zeigt. Die detaillierte Topographie der Oberfläche ist in enger Verbindung zur Auswertung zu sehen. Große Bedeutung hat daher die automatische Detektion von Steganteil und Näpfchentiefe.
Optische Walzenmikroskope
Geräte wie Kameras, Monitore und Messeinrichtungen liefern mit zugehöriger Software Rasterzahl, Steg-/Öffnungsbreite, und den Steganteil.
Volugraph
Der Farbabdruck auf der Rasterwalze wird mittels Planimeter gemessen. Durch eine Rakel wird Farbe in der Walzenoberfläche verteilt, um dann einen Abdruck auf Papier vorzunehmen. Ein Planimeter misst die Fläche der übertragenen Farbmenge auf der Walzenoberfläche und der Fläche Farbe auf dem Papier. Beide Werte ergeben das befindliche Schöpfvolumen. Der Zeitaufwand des Messvorganges liegt bei 20 Minuten für drei Messstellen. Die Messgenauigkeit liegt bei ±5 %.
Capatch
Der Capatch ist eine weitere Möglichkeit das Volumen von Raster- und Gravurenwalzen zu ermitteln. Zur Messung wird er auf die Rasterwalzenoberfläche aufgeklebt. Er enthält eine Kapsel mit einer Flüssigkeit, die durch überstreichen mit einer Rakel die Flüssigkeit aus der Kapsel presst. Die Länge des zurückgelegten Weges definiert das Volumen. Der Zeitaufwand der Messung ist gering bei 3 bis 4 Minuten und hat eine Messgenauigkeit von ±5 %.
Urmi
Urmi ist ein Walzen-Messgerät zur schnellen und genauen Bestimmung des Schöpfvolumens an lasergravierten Keramikrasterwalzen. Entwickelt wurde es zur Verringerung des Zeitaufwands bei der Optimierung der Druckqualität sowie zur Erhöhung der Messgenauigkeit für das Schöpfvolumen. Hierbei wird eine fluoreszierende Flüssigkeit im sichtbaren Bereich durch eine Rakel verteilt und in der Struktur der Walzenoberfläche gemessen. Der Anteil bestimmt die Menge an Flüssigkeit in der Struktur und damit auch das Schöpfvolumen. Die Messung ist auf einem trockenen und sauberen Teil der Oberfläche der Walze vorzunehmen, da das beleuchtende Licht sonst reflektiert wird. Das Licht würde erneut durch die fluoreszierende Flüssigkeit wandern und einen erhöhten Anteil ergeben. Um diesem vorzubeugen, sollte nach jedem Messvorgang die Indikator-Flüssigkeit mit einem Reinigungsmittel auf Basis von Naphthalin entfernt werden. Die Dauer der Messung ist schneller als mit dem Volugraph und hat eine Genauigkeit von ±5 %.
Weblinks
- Flexodruck Verfahren. Abgerufen: 21. April 2016
Literatur
- Helmut Kipphan: Handbuch der Printmedien – Technologien und Produktionsverfahren. 1. Auflage. Springer, Berlin 2000, ISBN 978-3-540-66941-8.
- Helmut Teschner: Druck & Medien Technik. 11. Auflage. Fachschriften Verlag, Fellbach 2003.
- K.-H. Meyer (Hrsg.): Technik des Flexodrucks. 5. erweiterte Auflage. Rek & Thomas Medien AG, DFTA (Deutschsprachige Flexodruck Fachgruppe e. V.) St. Gallen 2006.
Einzelnachweise
- ↑ K.-H. Meyer (Hrsg.): Technik des Flexodrucks. 5. erweiterte Auflage. Rek & Thomas Medien AG, DFTA (Deutschsprachige Flexodruck Fachgruppe e. V.) St. Gallen 2006, S. 70.
- ↑ a b c Helmut Kipphan: Handbuch der Printmedien – Technologien und Produktionsverfahren. 1. Auflage. Springer, Berlin 2000, ISBN 978-3-540-66941-8, S. 415 f.
- ↑ a b c d e f Patrick Hogan: Aniloxes – Yesterday, Today and Tomorrow. In: labe & Narrow Web Magazine. 16. November 2018, abgerufen am 26. Januar 2025 (englisch).
- ↑ Flexo- und Tiefdruck, Fachzeitschrift, Sonderausgabe, DFTA-Jubiläum Stand September 2004, S. 62–65.
- ↑ Ana Gomez: A Historical essay on the development of flexography. (PDF; 8,7 MB) Master’s Thesis. In: repository.rit.edu. Rochester Institute of Technology, 1. Februar 2000, abgerufen am 26. Januar 2025 (englisch).
- ↑ K.-H. Meyer (Hrsg.): Technik des Flexodrucks. 5. erweiterte Auflage. Rek & Thomas Medien AG, DFTA (Deutschsprachige Flexodruck Fachgruppe e. V.) St. Gallen 2006.
- ↑ Ansgar Wessendorf: Windmöller & Hölscher: 70 Jahre Zentralzylinder-Flexodruckmaschinen. In: VerpackungsDruck & Converting. Ebner Media Group, 16. Dezember 2024, abgerufen am 27. Januar 2025.
- ↑ a b Helmut Teschner: Druck & Medien Technik. 11. Auflage. Fachschriften Verlag, Fellbach 2003, S. 10.22
- ↑ Helmut Teschner: Druck & Medien Technik. 11. Auflage. Fachschriften Verlag, Fellbach 2003, S. 664.
- ↑ In: Flexo- und Tiefdruck. Ausgabe 2-2005, S. 4–11.
- ↑ Know-how with a high technology content – since 1979. In: flexxoprintingsolution.com. Flexxo Sas, 2019, abgerufen am 29. Januar 2025 (englisch).
- ↑ a b Andreas Ihme: Einfärbung im Flexodruck – Möglichkeiten zur Standardisierung der Prüfmethoden für Rasterwalzen. (PDF; 4,2 MB) In: druckingenieure.de. Verein Deutscher Druckingenieure, 2016, abgerufen am 2. Februar 2025.
- ↑ Surface finishing. In: zecher.com. Abgerufen am 3. Februar 2025.
- ↑ Ceramic and chrome anilox rollers – Unique treatments. (PDF; 669 kB) In: ulmex.com. Februar 2024, abgerufen am 3. Februar 2025 (englisch).
- ↑ K.-H. Meyer (Hrsg.): Technik des Flexodrucks. 5. erweiterte Auflage. Rek & Thomas Medien AG, DFTA (Deutschsprachige Flexodruck Fachgruppe e. V.) St. Gallen 2006, S. 72.
- ↑ K.-H. Meyer (Hrsg.): Technik des Flexodrucks. 5. erweiterte Auflage. Rek & Thomas Medien AG, DFTA (Deutschsprachige Flexodruck Fachgruppe e. V.) St. Gallen 2006, S. 65.
- ↑ a b Steve Woodard: Shape, Volume, Count: Standard Anilox Specifications in Flexographic Packaging. In: flexography.org. Flexographic Technical Association, abgerufen am 7. Februar 2025 (englisch).
- ↑ The geometry of an anilox. In: flexotechmag.com. Whitmar Publications, 1. April 2016, abgerufen am 7. Februar 2025 (englisch).
- ↑ a b Herausforderungen des High Quality Flexodrucks. (PDF; 2 MB) In: wirsindfarbe.de. Fachgruppe Druckfarben im Verband der deutschen Lack- und Druckfarbenindustrie e. V., 2016, abgerufen am 18. Februar 2025.
- ↑ a b Shonk: From Art to Science: The Evolution of the Anilox. In: pamarco.com. 6. Januar 2015, abgerufen am 7. Februar 2024 (englisch).
- ↑ a b c Frank van den Berge: Laser Engraving of Anilox Rolls: The Next Paradigm Shift. In: flexoexchange.com. Dezember 1997, abgerufen am 13. Februar 2025 (englisch).
- ↑ Stephan Brüning: High performance laser processing of most precise anilox rollers. In: VerpackungsDruck & Converting. Ebner Media Group, 14. Dezember 2023, abgerufen am 13. Februar 2025.
- ↑ Fachzeitschrift. In: Flexo- und Tiefdruck. Ausgabe 2-2005, S. 4–9.
- ↑ Roland Golpon: Elektronische Zylindergravur. (PDF; 4,7 MB) aus dem Lehrbuch Tiefdruck-Lehrbuch Band 2. In: hell-kiel.de. Verein der Freunde und Förderer Technische Sammlung Dr.-Ing. Rudolf Hell in Kiel e. V., 1968, abgerufen am 21. Januar 2025.
- ↑ Fachzeitschrift für den Verpackungsdruck: Flexoprint. Ausgabe Februar 1992, S. 19–21.
- ↑ a b Helmut Kipphan: Handbuch der Printmedien – Technologien und Produktionsverfahren. 1. Auflage. Springer, Berlin 2000, ISBN 978-3-540-66941-8, S. 265.
- ↑ Christian Dominic Fehling: 3. Lernmodul: Lackieren in Offsetdruckmaschinen (= Institut für Systemforschung der Informations-, Kommunikations- und Medientechnologie der Bergischen Universität Wuppertal [Hrsg.]: Handbücher für den Einsatz von Social Augmented Learning. Band 3). Zentral-Fachausschuss Berufsbildung Druck und Medien, Juli 2016, S. 9–12 (social-augmented-learning.de [PDF; 4,4 MB; abgerufen am 4. März 2025]).
- ↑ a b Siegfried Weiner, Reinhardt Dortschy, Günther Stoffel, Thomas Schmiedel, Werner Sondergeld: Leitfaden – Rasterwalze im Lackwerk. (PDF; 3,2 MB) Dortschy, archiviert vom am 3. Januar 2012; abgerufen am 4. März 2025.
- ↑ a b c d e f Ansgar Wessendorf: Rasterwalzen richtig reinigen. In: VerpackungsDruck & Converting. Ebner Media Group, 13. März 2018, abgerufen am 22. Januar 2025.
- ↑ a b Ansgar Wessendorf: Gängige Verfahren der Rasterwalzenreinigung. In: VerpackungsDruck & Converting. Ebner Media Group, 18. Januar 2018, abgerufen am 24. Januar 2025.
Auf dieser Seite verwendete Medien
Autor/Urheber: Rio kw, Lizenz: CC BY-SA 3.0
Rasterwalze – Volumen vs. Entleerungsverhalten
Autor/Urheber: ECTran71, Lizenz: CC BY-SA 4.0
Optical microscope true-color image of the hexagonal cells (dimples) engraved into the surface of an anilox roll. Each cell is about 100 microns across. Image taken using an Olympus OLS4100 confocal laser scanning microscope at 432x magnification.
Autor/Urheber: Rio kw, Lizenz: CC BY-SA 3.0
Grafisch vereinfachte Darstellung des Flexodruckprinzips am Beispiel des Kammerrakelsystems