Fließbandfertigung

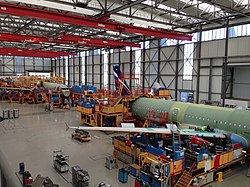
Die Fließbandfertigung (oder das Fließband) ist eine Fertigungsablaufart, die in der industriellen Fertigung von Massengütern angewendet wird. Sie stellt eine Spezialisierung der Fließfertigung dar, in der die Produkte jeweils einzeln, oft kontinuierlich, zur weiteren Bearbeitung von einem Arbeitsplatz zum nächsten befördert werden.
Fließfertigung
Bei der Fließfertigung (oder Reihenfertigung) wird die Herstellung eines Produktes in aufeinanderfolgende Arbeitsprozesse unterteilt, die wiederum in einzelne Arbeitsschritte aufgeteilt sein können. Die Aufstellung der Betriebsmittel folgt diesem Produktionsablauf, die Maschinen und Werkzeuge werden am Arbeitsplatz so angeordnet, wie es die Abfolge des Arbeitsprozesses erfordert. Das bekannteste Beispiel für die Fließbandfertigung sind die Montagebänder im Automobilbau, die in Montage-Takte unterteilt sind.
Die Fließbandfertigung ist eine Weiterentwicklung bzw. Spezialisierung der Fließfertigung. Bei dieser sind die Betriebsmittel oder Arbeitsplätze ebenfalls bereits in der Reihe angeordnet wie es der Arbeitsfolge entspricht. Bei der Fließfertigung erfolgt die Förderung jedoch noch losweise. In beiden Konzepten sind die Arbeitsgänge zeitlich vorbestimmt. Bei der Fließbandfertigung muss – bei fester Verkettung – die vorgeschriebene „Taktzeit“ eingehalten werden.
Die Planung und Durchführung der Fertigung erfolgt dem Produkt (Werkstück), also nach Objektprinzip.
Fließproduktion
Eine Fließproduktion ist zumeist verfahrenstechnisch bedingt. Die Anordnung der Produktionsstellen ist eine zwangsläufige Folge technologischer Gegebenheiten des Produktionsprozesses, etwa bei der Rohölverarbeitung in Raffinerien oder der Stahlerzeugung oder organisatorischen Überlegungen zu Grunde liegen.
Fließbandfertigung

Bei der Fließbandproduktion als konsequentester Ausprägung der Fließfertigung erfolgt der Materialtransport zwischen den einzelnen Produktionsstellen mit Hilfe von verketteten Fördersystemen (zum Beispiel Förderbändern) in der Losgröße eins. Die einzelnen Arbeitsschritte werden dabei meist auf wenige Handgriffe reduziert. In der klassischen Form ist ein Arbeitsschritt eine permanente Wiederholung einer genau determinierten Handgrifffolge.
Die ausführenden Arbeitsgänge und der Transport zwischen den Produktionsstellen erfolgen im festen zeitlichen Rhythmus. Dadurch ist die Bearbeitungsdauer an den einzelnen Stationen voneinander abhängig. Man spricht von einer zeitlich gebundenen Fließfertigung.
Entscheidend für den reibungslosen Ablauf ist ein optimaler Fließbandabgleich:
Die einzelnen Arbeitsschritte und Arbeitsstationen müssen so festgelegt werden, dass ihre Durchführung genau eine festgelegte Zeitdauer benötigt, die Taktzeit. Durch diese Vorgabe eines festen Fertigungsablaufs können Termin- und Kapazitätsplanungsprobleme effizient gelöst werden, das produktivste Herstellungsverfahren wird gewissermaßen erzwungen.
Erfolgt eine automatisierte Verkettung der Produktionsstellen, spricht man von einer (starren) Transferstraße, der Produktionsprozess erfolgt vollautomatisch.
Durch die oft hohe Anlagenintensität kommt diese Art der Fertigung vor allem bei der Sorten- und Massenproduktion zur Anwendung. Durch die geringe Flexibilität – der Produktaufbau darf keinen kurzfristigen Veränderungen unterliegen – ist zudem eine gesicherte Marktanalyse vorauszusetzen.
Dafür können die variablen Kosten relativ niedrig gehalten werden (niedrige Kosten des Lagers und Transports, der Fertigung und Löhne, wenig Ausschuss und Abfall).
Verwendung findet die Fließbandfertigung beispielsweise in der Automobilfertigung, dem Verlags- und Druckergewerbe und der Nahrungsmittelindustrie.
Vorteile
- Halbfertigerzeugnisse werden auf ein Minimum reduziert, dadurch können Zwischenlager weitgehend vermieden werden.
- Auch die konsequente Anordnung der Arbeitsplätze spart Raum, dazu werden Transportwege verkürzt, Transportkosten verringert
- (Kosten-)Vorteile durch Arbeitsteilung und Spezialisierung
- Niedrige Durchlaufzeiten ermöglichen eine Verringerung der Gesamtfertigungszeit
Nachteile
- geringe Flexibilität bei Beschäftigungsschwankungen, die Anpassungsfähigkeit des Betriebs ist herabgesetzt
- hohe Störanfälligkeit der gesamten Produktion bei Maschinen- oder Arbeitsausfällen
- hohe Anlagenintensität
- oft geringe Handlungsspielräume der Arbeitskräfte
- monotone Arbeit erzeugt Entfremdung, Abstumpfung und Motivationsprobleme
- mangelnde Kommunikationsmöglichkeiten erzeugen soziale Probleme der Arbeiter
Geschichte



Bereits im späten 15. Jahrhundert wurden im Arsenale Novissimo in Venedig Schiffe fließbandartig gefertigt. 1790 erhielt Oliver Evans ein Patent auf eine Mühle, in der verschiedene Techniken des kontinuierlichen Transports angewandt wurden. Im Jahr 1833 wurde bei der Herstellung von Schiffszwieback in England ein Fließband eingeführt. Um das Jahr 1870 wurden in den Schlachthöfen von Cincinnati hochgelegte Transportbänder eingesetzt, um die geschlachteten Schweine von einem Arbeiter zum nächsten zu transportieren. Diese Technik wurde in den Union Stock Yards Chicagos perfektioniert und in großem Stil angewandt. Die sogenannten „disassembly lines“ waren auch ein Vorbild für die „assembly lines“ zur Produktion des Fords T.[1]
In Deutschland setzte die Firma Bahlsen bereits im Jahr 1905 das Fließband ein.[2]
Ransom Eli Olds verwendete bereits 1902 für die Produktion seiner „Oldsmobile“ bewegliche Holzgestelle (wheeled carts), auf denen die Fahrgestelle von Station zu Station geschoben wurden.[3] Henry Ford mechanisierte und verfeinerte dieses Prinzip, indem er mit Hilfe seines Ingenieurs Charles E. Sorensen und des Vorarbeiters Lewis im Jahr 1913 ein permanentes Fließband aufbaute und so die erste „moving assembly line“ installierte.[4][5] Dadurch steigerte Ford die Produktion auf das Achtfache, so dass er zugleich den Preis seines T-Modells („Tin Lizzy“ bzw. „Blechliesel“ genannt) enorm verringern und die Löhne erhöhen konnte.[6]
Aufgrund seines Erfolges baute er nach diesem Prinzip eine ganz neue Fabrik am River Rouge in Detroit, die zu einem Mekka für Ingenieure und Automobilhersteller aus aller Welt wurde. Viele von ihnen übernahmen anschließend die Produktionsprinzipien Henry Fords wie zum Beispiel Fiat, Renault oder Volvo. In Deutschland wurde die Fließbandproduktion im Automobilbau in den 1920er Jahren zuerst von Brennabor sowie von der Firma Adam Opel mit dem „Laubfrosch“ und von der Firma Hanomag mit dem „Kommissbrot“ eingeführt.[7] Die Daimlerwerke führten diese Art der Fertigungsorganisation erst in den 1930er Jahren durch Wilhelm Friedle ein, der Betriebsdirektor der Daimler-Benz AG im Werk Sindelfingen war. Das Volkswagenwerk in Wolfsburg, in dem der KdF-Wagen gebaut werden sollte, wurde in den dreißiger Jahren ebenfalls ganz nach dem Vorbild der Ford-Fabrik am River Rouge konzipiert.
Die Fließbandfertigung ist im Automobilbau immer noch aktuell, und das Fließprinzip wird ständig ausgeweitet. Ein Beispiel dafür ist die Just-in-time-Produktion, bei dem die Fließfertigung bis zum Lieferanten und teilweise sogar bis zum Vorlieferanten ausgedehnt wird.[8] Auch etliche Unternehmen in anderen Industriezweigen, wie die Flugzeugindustrie (zum Beispiel Boeing) und der Maschinenbau (zum Beispiel Gildemeister, Trumpf), stellen ihre Produktion zunehmend auf die Fließfertigung um. Die Fließfertigung ist eine der wesentlichen Grundlagen die Einführung des Pull-Systems und für verschiedene Methoden und Verfahren der Produktionsplanung und -steuerung wie zum Beispiel das Verfahren der Fortschrittszahl oder Kanban.
Das anfängliche Willkommen des als revolutionär gefeierten Fließbandes schlug bald in starke Ablehnung um. Die mechanischen Arbeitsprozesse, denen sich die Arbeiter ausgesetzt sahen, führten zu einer Abstumpfung und zur Entwertung der Arbeitskraft, da nur noch wenige, monotone Handgriffe des Einzelnen nötig waren.
Die sogenannte Humanisierung der Arbeitswelt führte zu einer veränderten Prozessführung von Fließbandarbeit. Die Arbeitsschritte werden in Gruppen ausgeführt (Gruppenarbeit/Gruppenfertigung) und der Akkord (Arbeitsleistung) bezieht sich auf eine Gruppe von Arbeitern (Werktätige, gewerbliche Mitarbeiter).
Der Schauspieler Charlie Chaplin hat die Arbeit am Fließband in seinem Film „Moderne Zeiten“ (Modern Times) eindrucksvoll dargestellt.
Siehe auch
- Fließbandabstimmung
- Chaku-Chaku
- Fertigungslinie
- Fertigungsstraße
- Heijunka
- Heikinka
- Wandlungsfähige Produktionssysteme
- Nivellierung
- Serienproduktion
- Taylorismus
- Steinkühlerpause
- Springer (Taktarbeit)
Literatur
- Henry Ford: Erfolg im Leben – Mein Leben und Werk. List Verlag, München 1952.
- Helen Jones Earley, James R. Walkinshaw: Setting the Pace – Oldsmobile’s first 100 Years. Oldsmobil Division of GM Verlag, Lansing 1996, ISBN 0-7853-1958-1.
- Wolfgang Domschke, Armin Scholl, Stefan Voß: Produktionsplanung. 2. Auflage. Springer-Verlag, Berlin 2005, ISBN 3-540-63560-2.
- Russ Banham: Das Ford-Jahrhundert. Tehabi Books, San Diego 2002, ISBN 1-887656-91-X.
- Wilmjakob Herlyn: PPS im Automobilbau – Produktionsprogrammplanung und -steuerung von Fahrzeugen und Aggregaten. Hanser Verlag, München 2012, ISBN 978-3-446-41370-2.
- Wolfgang Holle: Rechnerunterstützte Montageplanung – Montageplanung und Simultaneous Engineering. Hanser Verlag, München 2002, ISBN 3-446-21986-2.
- David E. Nye: America’s Assembly Line. MIT Press, Cambridge/London 2013, ISBN 978-0-262-01871-5.
- Mario Steinbrink: Übergang zur Fließarbeit und Fließbandproduktion in den „Gebr. Reichstein Brennabor-Werke Brandenburg/Havel“, VFV-Info 2/2016
Weblinks
Einzelnachweise
- ↑ Die Erfindung des Schlachtplans. Archiviert vom am 3. April 2015; abgerufen am 17. Februar 2022. Info: Der Archivlink wurde automatisch eingesetzt und noch nicht geprüft. Bitte prüfe Original- und Archivlink gemäß Anleitung und entferne dann diesen Hinweis.
- ↑ Die Bahlsen-Chronik ( vom 5. August 2013 im Internet Archive)
- ↑ H. J. Earley, J. R. Walkinshaw: Setting the Pace. Lansing 1996, ISBN 0-7853-1958-1, S. 37.
- ↑ Henry Ford: Erfolg im Leben. Paul List Verlag, München 1952, S. 48 ff.
- ↑ Banham: Das Ford Jahrhundert. Tehabi books, San Diego 2002, ISBN 1-887656-91-X, S. 37 ff.
- ↑ Henry Ford: Erfolg im Leben. Paul List Verlag, München 1952, S. 94 ff.
- ↑ Herlyn: PPS im Automobilbau. Hanser Verlag, München 2012, ISBN 978-3-446-41370-2, S. 24 ff.
- ↑ Herlyn: PPS im Automobilbau. Hanser Verlag, München 2012, ISBN 978-3-446-41370-2, S. 34–46.
Auf dieser Seite verwendete Medien
1913 photograph Ford company, USA
Autor/Urheber: Manfed Kopka, Lizenz: CC BY-SA 4.0
Fließbandproduktion des VW Käfers in Wolfsburg
Autor/Urheber: User: Anonyme , Lizenz: CC BY 2.5
Assembly line at Hyundai Motor Company’s car factory in Ulsan, South Korea.
Pork packing in Cincinnati. Print showing four scenes in a packing house: "Killing, Cutting, Rendering, [and] Salting." Chromo-lithograph of the cartoons exhibited by the Cincinnati Pork Packers' Association, at the International Exposition, at Vienna. Entered according to Act of Congress in the year 1873 by Ehrgott & Krebs in the Office of the Librarian of Congress at Washington, D.C.
Autor/Urheber: DearEdward from New York, NY, USA, Lizenz: CC BY 2.0
Final assembly line 3 at Airbus' Hamburg plant. The model for the Tianjin and under construction Mobile FALs.