Schwingbruch
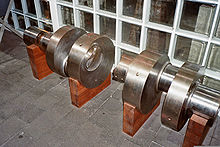

an einer gegossenen Aluminium-Fahrradkurbel;
hell: Gewalt- bzw. Sprödbruch

In der Bruchfläche sind die Zonen des Bruches zu erkennen: links ein schon länger bestehender Anriss (dunkel); zur Mitte hin der Bereich des unter Wechselbelastung fortschreitenden Ermüdungsbruches mit Rastlinien, von rechts eine weitere Ermüdungsbruchzone, dazwischen die schmale Gewaltbruchzone
Als Schwingbruch[1], Schwingungsbruch oder umgangssprachlich Dauer- oder Ermüdungsbruch, bezeichnet man den Bruch unter Lastwechselbeanspruchung. Die meisten Brüche im Maschinenbau lassen sich hierauf zurückführen.
Die Ermüdung des Bauteils, an dessen Ende sein Versagen oder sein Bruch steht, hängt vor allem ab von der Dauer und der Intensität der wechselnden Belastung: je höher die Frequenz und je größer die Amplitude der Schwingung, desto früher der Schwingbruch. Qualitativ lässt sich die Höhe der Belastung ableiten aus dem Verhältnis der Schwingbruchfläche zur Restgewaltbruchfläche: je größer die Restgewaltbruchfläche, desto höher war die auf den Werkstoff einwirkende Nennspannung.
Im Unterschied zum Gewaltbruch wirken auf den Werkstoff Spannungen bedingt durch schwellende oder schwingende Belastung ein, die unterhalb der Streckgrenze, also im elastischen Bereich, liegen.
Unter solchen Wechselbeanspruchungen lassen sich bei einer ausreichenden Zahl von Lastwechseln Veränderungen in der Mikrostruktur des Werkstoffes feststellen, die ein Indiz für die Ermüdung sind:
- Sichtbares Kennzeichen für einen Ermüdungsbruch sind Rastlinien auf der Bruchfläche aufgrund intermittierenden Risswachstums.
- Das mikroskopische Gegenstück dazu sind sehr fein strukturierte Furchen, die als Schwingstreifen bezeichnet werden. Nach der Theorie lässt sich anhand des Abstandes zweier Schwingstreifen ein Lastwechselzyklus bestimmen, dies ist aber in der Praxis nur sehr selten möglich, da z. B. keine vollständig gleiche Schwingungsbelastung vorliegt. Schwingstreifen sind ein fast sicheres Indiz für eine zyklische Beanspruchung, dürfen jedoch nicht mit dem Bruch eines perlitischen Gefüges verwechselt werden.
Meist reichen Rastlinien sowie die Art des Bruchverlaufes aus, um einen Schwingbruch nachzuweisen.
Maßnahmen zur Vermeidung
Da die Ursache für den Schwingbruch letztlich die mechanische Wechselspannung ist, gilt es diese durch konstruktive Maßnahmen zu vermindern:
- ausreichende Dimensionierung des Bauteils auf dynamische Beanspruchung, etwa durch Dimensionierung gegen Bauteilversagen an der schwächsten Stelle unter Zuhilfenahme von Smith- oder Haigh-Diagrammen, Wöhlerlinien-Schaubildern oder durch Betriebsfestigkeits-Kalkulationen oder maschinendynamische Berechnungen
- Vermeiden zusätzlicher wechselnder Spannungen infolge von Eigenschwingungen.
Die Eigenschwingungen, die durch den Lastfall oder eine Fremderregung bewirkt werden können, können die alleinige Ursache eines Ermüdungsbruches sein. Ein Beispiel sind hochstehende schwere bedrahtete elektronische Bauelemente auf Leiterplatten, die z. B. in Kraftfahrzeugen oder an schwingenden Maschinen eingesetzt werden, oder auch Schutzbleche und deren Halterungen an Fahrrädern. In solchen Fällen ist es sinnvoll, die Eigenfrequenz des schwingungsfähigen Systems zu ändern (vorzugsweise durch höhere Steifigkeit) oder die Schwingung zu dämpfen. Auf Leiterplatten werden bedrahtete, hochstehende Bauteile daher oft mit Klebstoff festgelegt.
Neben der Dimensionierung des Bauteiles vermindert man die Gefahr des Schwingbruches im Maschinenbau, indem man vor allem dort, wo eine hohe örtliche Spannung herrscht, einen Ausgangspunkt für den Bruch vermeidet durch:
- Vermeiden abrupter Querschnittsänderungen, Schaffen gerundeter Übergänge
- Vermeidung von Kerben, z. B. infolge von
- Beschädigungen
- konstruktiven Elementen wie Gewinden und Nuten
- fertigungstechnischen Besonderheiten wie unbearbeiteten Schweißnähten
- Schaffen glatter Oberflächen
- Einbringung von Druckeigenspannungen in die Werkstoffoberfläche; gebräuchlich ist hier das Kugelstrahlen, was wissenschaftlich nachweisbar Druckeigenspannungen in den Werkstoff einbringt und die Lebensdauer bei zyklischer Beanspruchung verlängert

- Behandlung von Schweißnahtübergängen mit dem High Frequency Impact Treatment (kurz HiFIT)–Verfahren zur Lebensdauerverlängerung von Schweißkonstruktionen durch Ausrunden der geometrischen Kerbe, Oberflächenglättung, Randschichtenverfestigung und Einbringen von Druckeigenspannungen bis zu einer Tiefe von 1,5 mm
- Vermeiden von Herstellungsfehlern wie Dopplungen und Einschlüssen
- Verwenden geeigneter Werkstoffe – so nimmt man an, dass z. B. Gusseisen mit Kugelgraphit gegenüber Lamellenguss einen günstigeren Spannungsverlauf im Mikrogefüge bewirkt
- Korrosionsschutz, u. a. um Spannungsrisskorrosion zu vermeiden.
Einzelnachweise
- ↑ gemäß VDI-Richtlinie 3822
Siehe auch
Auf dieser Seite verwendete Medien
Autor/Urheber: Markus Schweiss, Lizenz: CC BY-SA 3.0
Ermüdungsbruch einer Kurbelwelle; entstanden im Rheinischen Industriemuseum, Oberhausen
Autor/Urheber: Dynatec, Lizenz: CC0
Example of a HiFIT-treated assembly.
Autor/Urheber: Lokilech, Lizenz: CC BY-SA 3.0
Ermüdungsbruch meines Fahrradpedalarmes (Kettler Alu-Rad von etwa 1990), hell: der Spröd-, Gewaltbruch, dunkel: der Ermüdungsbruch mit Rastlinien
broken bolt from a wheel of a lorry / gebrochener Radmutternbolzen von einem LKW